In a world where efficiency and precision are paramount, RNSinox emerges as a pioneer in the field of metallic transformation, adopting one of the most advanced technologies in robotic welding: the TIG LORCH system with cobot from Universal Robots. This article dives into the heart of this revolutionary decision, exploring how TIG robotic welding is redefining quality and efficiency standards in metal fabrication.
Article Content
Innovation and efficiency in robotic welding
Welding has always been a delicate art, combining skill, precision and knowledge. At RNSinox, this combination reaches a new level with the incorporation of TIG Cobot welding, an automated welding modality that is marking a before and after in the industry. This system not only represents an evolution in welding technique but is also a testament to RNSinox's constant pursuit of innovation and excellence.
The TIG LORCH Cobot: A technological ally
The Cobot TIG LORCH from Universal Robots stands out for its ability to automate the TIG welding process in the manufacturing of metal parts, from small series to large productions. What makes this technology unique is its flexibility and adaptability, allowing for high-precision welding. This feature not only optimizes the welding process, but also ensures consistent, high-quality results.
Human control with robotic precision
One of the biggest advantages of Cobot TIG welding is the combination of human control with robotic precision. Although the system is automated, the welder maintains full control, guiding the Cobot through the complexities of the welding process. This collaboration between man and machine ensures that each weld meets the highest standards, reducing the possibility of errors and rework, while increasing operator safety.
Benefits of Automated Welding
The adoption of automated welding at RNSinox brings multiple benefits. Among them, the notable optimization of the final quality of the products, with perfect finishes that satisfy the highest demands. Furthermore, this technology contributes to a significant cost reduction and increased productivity, thanks to the efficiency and speed of the automated process. Another crucial aspect is the safety of the operators, which is increased by reducing direct exposure to the risks of traditional welding.
A comprehensive 360 service in metal transformation
The choice of RNSinox for TIG Cobot welding is not an isolated event, but part of a comprehensive 360 service that the company offers in fine boilermaking. This approach ensures that all of its clients' metal processing needs are met efficiently and with the highest quality. From laser and TIG/MIG welding to resistance and automated welding, RNSinox is positioned as an exceptional supplier for any requirement in the manufacturing of metal parts.
A commitment to the future of metal processing.
By adopting automated welding, RNSinox not only improves its current manufacturing processes but also aligns itself with future industry trends. The incorporation of the Cobot TIG LORCH demonstrates a clear commitment to innovation and a step towards the future of metal manufacturing.
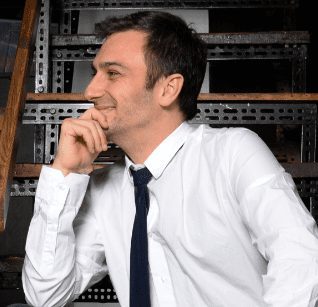
Expert in SEO/SEM and communication on social networks.
CEO at tecnologia.net and passionate about everything related to technological progress